Global Welding Market Progress Analysis to 2025: Focus on China, Europe and Nort
Release Date:2025/03/19
In the wave of deep change and industrial upgrading of the global manufacturing industry, the welding market, as a key support area for industrial development, is experiencing unprecedented opportunities and challenges. This analysis examines the development of the global welding market in 2025, focusing on the three core markets of China, Europe and North America, and provides insights into their market size, growth trends, technological innovations, and the opportunities and challenges they face. International welding system certification plays an integral role in the development and integration of global welding (AWS, ASME, EN ISO and other relevant welding standards are increasingly important).
I. Overall global market trends
(i) Market size and growth
Welding Equipment Market
The global welding equipment market has maintained a steady pace of development over the past few years. Back to 2023, its market size has already reached 19.72 billion U.S. dollars, this data intuitively demonstrates the welding technology in the construction, automotive, energy and other industries indispensable position. Looking ahead, in terms of market development trends, the welding equipment market size is expected to continue expanding at a CAGR of 5.1% through 2030.
In the construction sector, accelerating urbanization and the emergence of infrastructure construction projects have resulted in a large number of steel structures that need to be erected through welding processes. For example, in the construction of skyscrapers in many cities, welding technology ensures a solid connection between each steel beam, laying the foundation for the safety and stability of the building.
Automobile manufacturing industry as an important application field of welding equipment, with the steady rise of automobile production, especially the rise of new energy vehicles, the demand for welding equipment shows a diversified and high-end trend. New energy vehicles to achieve lightweight design, a large number of aluminum alloys, magnesium alloys and other lightweight materials, the welding of these materials requires more advanced, more sophisticated welding equipment.
Energy industry, whether it is the traditional oil, natural gas pipeline laying, or emerging wind power, solar power plant construction, welding technology plays a crucial role. In the construction of oil pipelines, high-quality welding ensures the safe transportation of crude oil; in wind power plants, welding technology firmly connects huge towers and blades together, guaranteeing the stable operation of wind turbines.
Welding Gases/Shielding Gases Market
The welding gases/shielding gases market size was estimated at USD 3.06 billion in 2024, while the future growth potential is projected to be substantial in the long run. The market size is expected to grow significantly to USD 5.99 billion by 2032, at a CAGR of 8.74%.
The booming new energy vehicle industry is one of the core drivers for the growth of the welding gas market. In the production process of lithium batteries, the electrode and battery components of the welding of gas purity and composition has strict requirements, the precise use of specific welding gas can effectively improve the performance and safety of the battery. Tesla, for example, is extremely strict in the selection and control of welding gases in the welding process of battery packs to ensure the high energy density and long service life of batteries.
In aerospace and high-end machinery manufacturing, specific protective gases are required to prevent oxidation and other defects when welding lightweight materials such as aluminum alloys and titanium alloys in order to ensure welding quality. In the manufacture of aero-engines, the use of welding shielding gases ensures high-quality welding between high-temperature alloy components and meets the performance requirements of engines under extreme operating conditions.
Welding Fume Purification Equipment
With the continuous awakening of global environmental awareness and increasingly stringent environmental regulations, the welding fume purification equipment market has also ushered in a good opportunity for development. Its market size is expected to reach USD 60.81 million by 2025. Asia-Pacific region, especially China, with the huge scale of manufacturing and extensive demand for welding operations, the demand for welding fume purification equipment in the context of the tightening of environmental regulations has shown explosive growth, occupying 50% of the global market share.
In China, many manufacturing enterprises in order to meet environmental standards, have invested a lot of money to buy advanced welding smoke purification equipment. These equipments can not only effectively filter the harmful gases and particles produced during the welding process, improve the working environment of workers, reduce the risk of occupational health, but also reduce the pollution of the surrounding environment and realize the sustainable development of enterprises. Some large-scale steel enterprises in the production workshop installed a highly efficient welding fume purification system, so that the air quality in the workshop has been significantly improved, but also to meet the strict requirements of the local environmental protection department.
(ii) Direction of technological innovation
Intelligent and automation
Intellectualization and automation have become the core trend of welding technology development. In the context of Industry 4.0 and intelligent manufacturing, welding robots are more and more widely used in industrial production due to their high precision, high efficiency and stable and reliable characteristics. They can accurately complete a variety of complex welding tasks in accordance with preset programs, greatly reducing the impact of human factors on welding quality.
BMW's iFACTORY factory is a typical representative of intelligent welding. Through the introduction of advanced AI visual inspection technology, the welding robot can monitor the quality of the weld seam in the welding process in real time and accurately. Once deviations, porosity and other defects are detected in the weld seam, the robot can immediately and automatically adjust the welding parameters and make corrections, which greatly improves the welding quality and production efficiency, and ensures that the weld quality of the body of each BMW vehicle reaches the top standard.
Laser welding technology as an advanced welding process, with its high energy density, fast welding speed, small heat-affected zone and other significant advantages, in the automotive, electronics, aerospace and other industries have been widely used. In the field of automobile manufacturing, laser welding is commonly used in the connection of body structure parts, which can not only realize lightweight design, reduce the weight of the body, reduce energy consumption, but also improve the strength and safety of the body. In the electronics industry, laser welding can be used for precision electronic components welding, to meet the miniaturization of electronic products, high-precision production needs.
Green Welding
In order to actively respond to the global environmental protection policy and promote sustainable development, green welding technology is gradually becoming a new direction for the development of the industry. Compared with the traditional manual arc welding, gas shielded welding has the advantages of stable welding process, less smoke and spatter, etc. It can effectively reduce the pollution of the environment, while improving the welding quality and production efficiency.
Some companies are also committed to research and development of efficient fume purification system, such as a well-known German company developed a purification rate of up to 99% of the welding fume purification system. The system uses advanced filtration technology and intelligent control algorithms, can be produced in the welding process of harmful gases and particles for efficient filtration and purification, to meet the EU and China and other regions of the most stringent environmental policy requirements. More and more welding equipment manufacturers are beginning to focus on energy-saving design of equipment, through the use of new power supply technology and optimization of control algorithms, to reduce the energy consumption of the equipment in the process of operation, to achieve the green, low-carbon development of welding production.
II. Chinese Market: Policy Driven and Industrial Upgrading
(i) Policy support and foreign investment layout
Government strategy
As a key basic technology of manufacturing industry, welding technology is clearly listed as a strategic emerging industry, which is strongly supported by the national policy.2025 government work report emphasizes the importance of expanding opening up, actively creating a favorable investment environment, and attracting foreign investment to participate in the upgrading process of the domestic industrial chain in depth.
Henkel Group invested 900 million yuan to build an adhesive innovation center, this major initiative not only greatly enhance its R & D strength in the field of adhesives, but also welding-related adhesive technology innovation and development has injected a strong impetus to strongly promote China's manufacturing industry to the high-end, intelligent direction. The expansion of Schneider Electric's medium-voltage production base, through the introduction of international advanced production technology and management experience, has led to the comprehensive upgrading of the domestic industry in terms of technology, process and management, and improved the overall competitiveness of the industry.
Foreign Investment Confidence
Many multinational enterprises have continued to increase their R&D investment in China, fully demonstrating their firm confidence in the Chinese market and strategic determination for long-term development. Lilly has been increasing its investment in China in the field of pharmaceutical R&D. The continuous construction and development of its R&D center in China will help promote the application of welding technology innovation in the manufacturing of related medical equipment and meet the growing domestic demand for high-end medical equipment.
Dassault Systèmes plans to invest 1 billion euros over the next five years to focus on industrial software and digital transformation. This strategic investment will provide China's manufacturing industry with more advanced digital design, manufacturing and management solutions to promote the deep integration of welding technology and digital technology to promote welding production to intelligent, automated, digital direction of rapid development, and effectively improve the efficiency and quality of welding production.
(ii) Demand growth areas
New energy vehicles
The rapid rise of the new energy automobile industry for the welding market has opened up a broad space for development. In terms of lithium battery welding materials, the market size of copper welding wire etc. has successfully increased to 1.5 billion U.S. dollars in 2024. With the new energy vehicles on the range and safety performance requirements continue to climb, the energy density, stability and reliability of lithium batteries put forward more stringent requirements. This creates an urgent need for more advanced and better welding materials and technologies to ensure high-quality connections between battery components.
In order to realize the lightweight design of the body, while ensuring the strength and safety of the body, automakers are widely used in new materials such as high-strength steel and light alloys, and their welding needs have grown dramatically. For example, BYD uses advanced welding processes such as friction stir welding and laser welding to connect high-strength steel and light alloy materials in its new-energy vehicle body manufacturing, effectively improving the overall performance and quality of the body.
Construction and Energy
In the field of construction and energy, welding equipment is still widely used and indispensable. In the power industry, from the installation of substation equipment in the construction of power grids to the laying of power transmission lines, each link is inseparable from the support of welding technology. In the construction of oil and gas pipelines, welding quality is directly related to the safe operation and service life of the pipeline, the welding process and equipment requirements are extremely high.
In 2024, China's welding equipment market annual growth rate of 8%, of which the demand for energy-saving power supply growth is particularly prominent, with a growth rate of up to 10%. With the country's continued strong investment in the construction of energy infrastructure, as well as energy saving and emission reduction targets continue to strengthen, the market prospects for efficient, energy-saving welding equipment is extremely broad. For example, in some large-scale wind power projects, the use of new energy-saving welding equipment, not only to improve the welding efficiency, but also reduces energy consumption, to achieve a win-win situation of economic and environmental benefits.
(iii) Technological breakthroughs
Laser Welding
Handheld and automatic laser welding technology has become increasingly mature in China, and has been applied on a large scale in key areas such as new energy vehicle manufacturing. Take BYD as an example, in its battery pack welding production line, advanced laser welding technology realizes high-quality welding of battery pole piece and connecting piece through precise control of laser energy and welding parameters, which greatly improves the performance and reliability of the battery pack. Laser welding technology plays a key role in the manufacturing of new energy vehicles by virtue of its fast welding speed, beautiful weld seam, no need for filler material and many other advantages, which can effectively improve production efficiency, reduce production costs and improve product quality.
Green Technology
The localization of welding fume purification equipment production process continues to accelerate, Chinese companies such as Boying Special Welding through the establishment of factories in Vietnam, not only to successfully meet the domestic market demand for welding fume purification equipment, but also actively expand overseas markets, radiation to Southeast Asia. Domestic enterprises continue to increase investment in research and development, continue to improve product performance and quality, reduce production costs, so that the product has a strong competitive edge in the international market. Some companies developed welding dust purification equipment using advanced filtration technology and intelligent control algorithms, according to the actual conditions of welding operations automatically adjust the purification parameters, to ensure efficient purification effect at the same time, reduce the energy consumption of the equipment, to achieve the goal of energy saving and environmental protection.
III. The European market: high-end manufacturing and green transformation
(i) The role of German industry as a benchmark
Technology leadership
As the bright pearl of European industry, Germany has always occupied a leading position in the field of welding technology. Siemens' digital twin technology plays an irreplaceable key role in the virtual commissioning of welding production lines. By constructing a digital model of the welding process, it is possible to optimize and validate the welding process comprehensively and intensively before actual production. This innovative technology effectively reduces the commissioning time and cost in actual production, and significantly improves production efficiency and product quality.
BMW's iFACTORY factory is a perfect integration of AI vision inspection technology and welding production, realizing real-time and accurate monitoring of welding quality. The AI algorithm quickly analyzes the image data during the welding process, which can timely and accurately find welding defects and immediately start the automatic correction mechanism, ensuring that the welding quality of every BMW car reaches the top level of the industry, setting a model for the high-quality development of the automotive manufacturing industry.
Industrial Cooperation
The 2025 China-EU industrial study tour focused on the field of intelligent manufacturing, and the two sides actively carried out in-depth exchanges and cooperation, visiting Fraunhofer Association, BASF and other well-known organizations. Fraunhofer Association has profound technical accumulation, advanced R&D equipment and professional research team in welding technology research. Through close cooperation with Chinese enterprises and scientific research institutions, it can promote knowledge sharing and technology exchange in the field of welding technology innovation between the two sides, and jointly overcome welding technology problems and promote the cutting-edge development of welding technology.
As a giant in the global chemical industry, BASF has unique technological advantages and rich experience in the research and development of welding materials. Cooperation with Chinese enterprises will help to widely apply its advanced welding materials in more fields, enhance the technical level of China's manufacturing industry in the application of welding materials, and realize the complementary advantages and common development of the two sides at the industrial level.
(ii) Environmental protection regulations drive
Green welding standards
The European Union's “Industry 4.0” strategy of low-carbon welding equipment, environmental protection has put forward extremely strict requirements. In order to respond positively to this strategic goal, the German enterprises to take on the burden of leading the development of low fume laser welding system. The system through the laser parameters and welding process carefully optimized, significantly reducing the welding process fume generation, while further improving the welding quality and productivity.
Germany has also developed and implemented a series of stringent environmental regulations and standards for welding operations in the emission of pollutants in the strict limits and regulation. This has prompted companies to continuously increase investment in welding technology and equipment development, and actively adopt a more environmentally friendly, more efficient welding process, to promote the entire welding industry to the green, sustainable direction.
Energy transition needs
With the acceleration of the energy transition process in Europe, the welding demand for energy storage and new energy equipment has shown rapid growth. At The Smarter E Energy Show, a number of innovative solutions for electric vehicle welding were unveiled. These solutions adopt advanced welding technologies and materials, which can perfectly meet the welding requirements of EV battery packs, motors and other key components, providing strong technical support for the booming development of the new energy vehicle industry in Europe.
In the field of wind power, solar power and other new energy sources, welding technology is also being constantly innovated and upgraded to meet the needs of large-scale production and efficient and stable operation of new energy equipment. For example, in the manufacture of large-scale wind turbines, new welding processes and materials are used to ensure the strength and reliability of the connection between the tower and blades, and to improve the power generation efficiency and service life of wind turbines.
(iii) Market challenges
In the European market, localized operation is a major challenge for enterprises. Taking Risong Technology's establishment of a factory in Mexico as an example, the enterprise needs to fully consider factors such as the complex cultural differences and the high temperature operating environment in the region. Cultural differences may lead to obstacles in management communication, difficult to unify the work habits of employees and other issues, which requires companies to develop and implement effective cross-cultural management strategies to strengthen cultural integration and team building.
High-temperature operating environment puts forward higher requirements for the performance and reliability of welding equipment. Enterprises need to make targeted improvements and optimization of equipment, the use of high temperature resistant materials, optimize the heat dissipation design and other measures to ensure that the equipment in the harsh high temperature environment can be stable and reliable operation, to ensure the smooth progress of production.
IV. North American market: technological innovation and defense needs
(I) U.S. Market Dynamics
Automated equipment dominated
The U.S. welding market is dominated by automation equipment, and the penetration rate of welding robots is at a high level. Lincoln Electric launched the POWER MIG 215 MPi and other multifunctional equipment, with its advanced welding performance and intelligent control functions, can flexibly meet the diversified needs of different users in the industrial manufacturing and civil fields.
In the field of industrial manufacturing, the equipment can be used in automotive parts manufacturing, machining and other industries, to achieve efficient and accurate welding production; in the civilian field, it can be used for home renovation, small metal products processing, etc., to provide convenient and reliable welding solutions for ordinary consumers. Its intelligent control system can automatically adjust welding parameters according to different welding materials and process requirements, ensuring the stability and consistency of welding quality.
Defense and Infrastructure Investment
The federal government to increase defense spending for ships, submarines and other military manufacturing sector has brought new opportunities for development. In these military projects, welding technology is a key process to ensure the structural strength and sealing of equipment. For example, during the construction of aircraft carriers, a large amount of high-strength steel needs to be connected by high-precision welding process to withstand the huge water pressure and complex marine environment.
Meanwhile, the increase in investment in infrastructure construction has also promoted the application of welding equipment in construction projects such as bridges and roads. In bridge construction, welding technology is used to connect steel girders and piers to ensure the stability and safety of bridges; in road construction, welding equipment can be used to manufacture and install road signs, guardrails and other facilities.
(ii) Technology Competition Pattern
Active corporate mergers and acquisitions
Industry giants such as Lincoln Electric and Illinois Tool Works continue to expand their market share and enhance their market competitiveness through active corporate M&A activities. For example, ESAB's acquisition of Cutting Technologies realized rapid business expansion and product line enrichment and improvement by integrating the technology, market and resource advantages of both parties. Corporate mergers and acquisitions not only help enterprises to obtain advanced technology and mature market channels in a short period of time, but also optimize the allocation of resources, reduce production costs, and improve the profitability and risk-resistant ability of enterprises.
Material Innovation
North American companies have made a series of important breakthroughs in the welding process of high-strength steel, titanium alloys and other materials. 70% of the Boeing 787 fuselage uses laser welding technology. This innovative application not only realizes the lightweight design of the fuselage, effectively reduces the fuel consumption and operating costs of the aircraft, but also improves the overall strength and reliability of the fuselage, and enhances the performance and safety of the aircraft. Through the continuous research and development and application of new welding materials and processes, North American companies have maintained their technological leadership in aerospace, high-end equipment manufacturing and other fields.
V. Regional comparison and future outlook
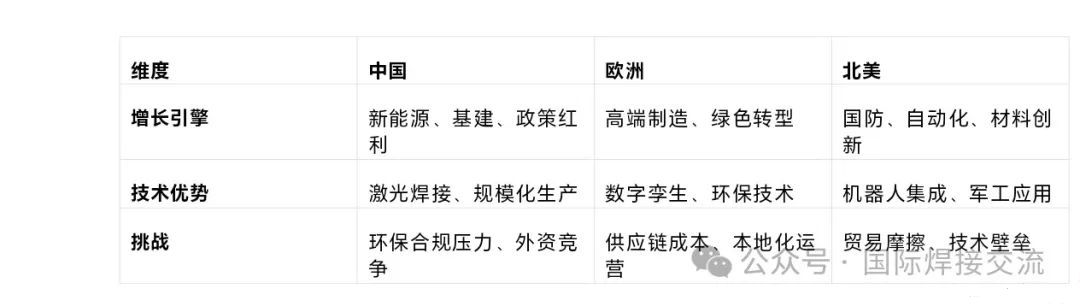
future trends
Global industry chain synergy: Chinese enterprises through the establishment of factories in Vietnam, Mexico and other places, and actively lay out the overseas market, make full use of local resources and market advantages; European and American enterprises to increase the investment in China's R & D, with China's huge market and rich talent resources, to achieve technological innovation and industrial upgrading. This mode of synergistic development of the global industrial chain will promote the in-depth cooperation and exchange between enterprises of different countries in welding technology and market, forming a good development pattern of complementary technology and resource sharing.
Carbon Neutral Goal: Under the background of the global active promotion of carbon neutral goal, green welding technology such as hydrogen welding will become the key direction of joint research and development between China, the United States and Europe. Through the research and development and application of green welding technology, can effectively reduce carbon emissions in the welding process, reduce the impact on the environment, to achieve sustainable development of the welding industry. At the same time, governments and enterprises will increase investment in green welding technology research and development, to promote rapid breakthroughs in related technologies and wide application.