These are the basics of laser cutting that you must master!
Release Date:2025/03/28
Lasers were first used for cutting as early as the 1970s. In modern industrial production, laser cutting is more widely used in sheet metal, plastics, glass, ceramics, semiconductors, textiles, wood and paper processing and other materials.
When the focused laser beam hits the workpiece, the irradiated area heats up dramatically to melt or vaporize the material. Once the laser beam penetrates the workpiece, the cutting process begins: the laser beam moves along the contour lines while melting the material. The molten material is usually blown away from the kerf by a jet of air, leaving a narrow slit between the cut part and the plate holder that is almost as wide as the focused laser beam.
flame cutting
Figure 1 The laser beam melts the workpiece and the cutting gas blows away the molten material and slag in the kerf.
Melt Cutting
Melt cutting is another standard process used when cutting metals. It can also be used to cut other fusible materials such as ceramics.
Compressed air cutting
Compressed air can also be used to cut thin plates. Air pressurized to 5-6 bar is sufficient to blow away the molten metal in the cut. Since nearly 80% of the air is nitrogen, compressed air cutting is essentially a melting cut.
Plasma-assisted cutting
If the parameters are properly selected, a plasma cloud will appear in the plasma-assisted fusion cutting kerf. The plasma cloud consists of ionized metal vapor and ionized cutting gas. The plasma cloud absorbs the energy of the CO2 laser and converts it into the workpiece so that more energy is coupled to the workpiece and the material will melt faster, resulting in a faster cutting speed. For this reason, this cutting process is also called high-speed plasma cutting.
The plasma cloud is in fact transparent with respect to solid-state lasers, so plasma-assisted melting cutting is only possible with CO2 lasers.
gasification cutting
Vaporized cutting vaporizes the material, minimizing the impact of thermal effects on the surrounding material. This can be achieved by using continuous CO2 laser processing to vaporize low-heat, high-absorption materials such as thin plastic films and non-melting materials such as wood, paper and foam.
Ultrashort pulsed lasers allow this technology to be applied to other materials. The free electrons in the metal absorb the laser and heat up dramatically. The laser pulse does not react with the molten particles and plasma, the material sublimates directly and there is no time for the energy to be transferred to the surrounding material in the form of heat. Picosecond pulses ablate the material with no visible thermal effect, no melting and no burr formation.
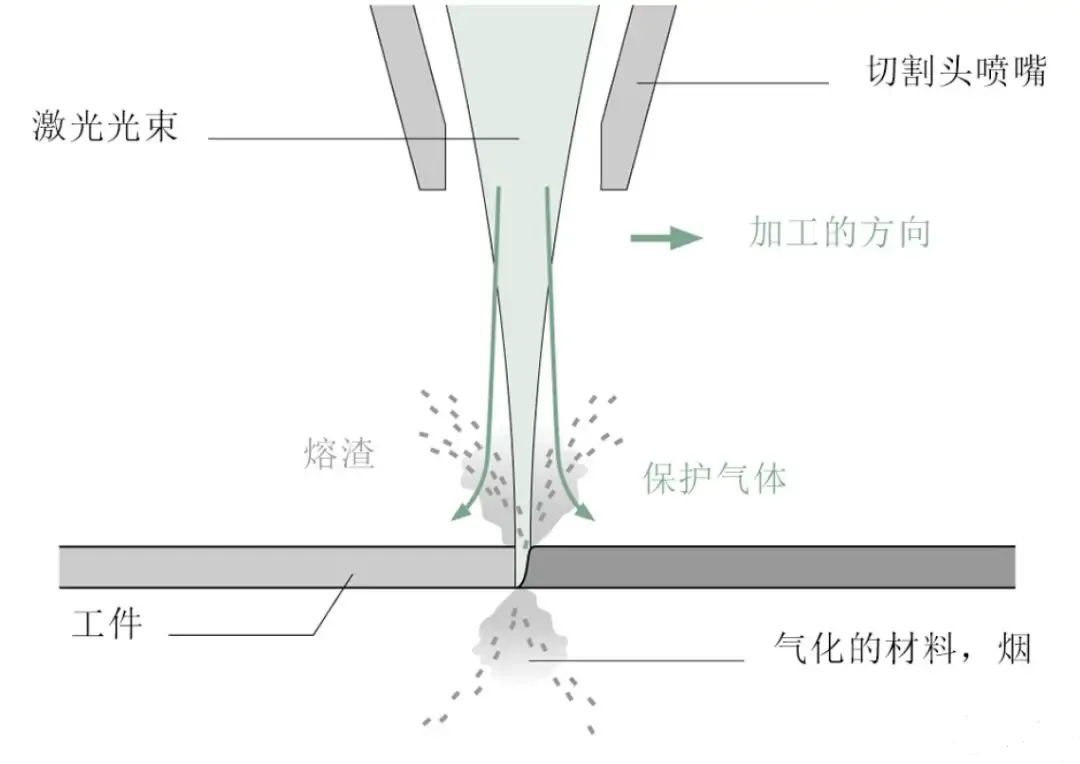
Parameters: Adjustment of the machining process
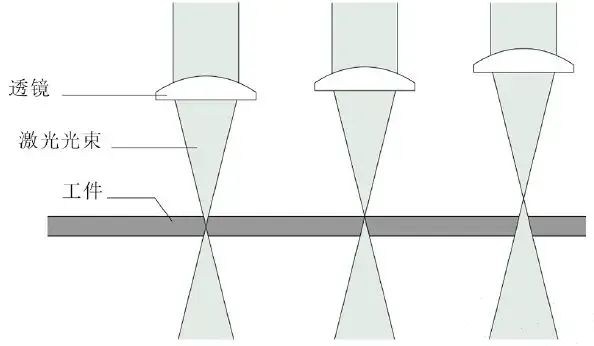
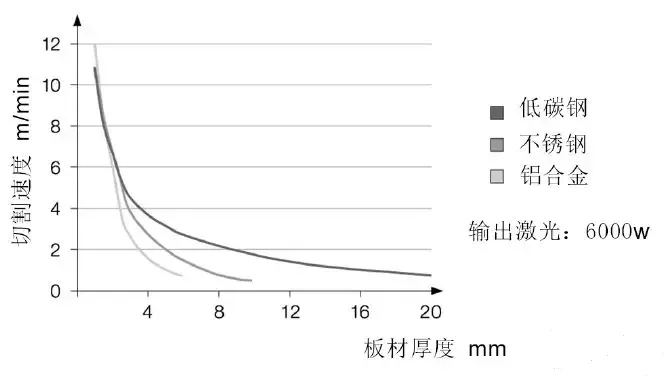
Oxygen and nitrogen are often used as cutting gases. The purity and pressure of the gas affect the cutting effect.
Laser cutting quality evaluation factors
Figure 7 Good cuts, bad cuts. Criteria for evaluating the quality of cut edges
panoramic view
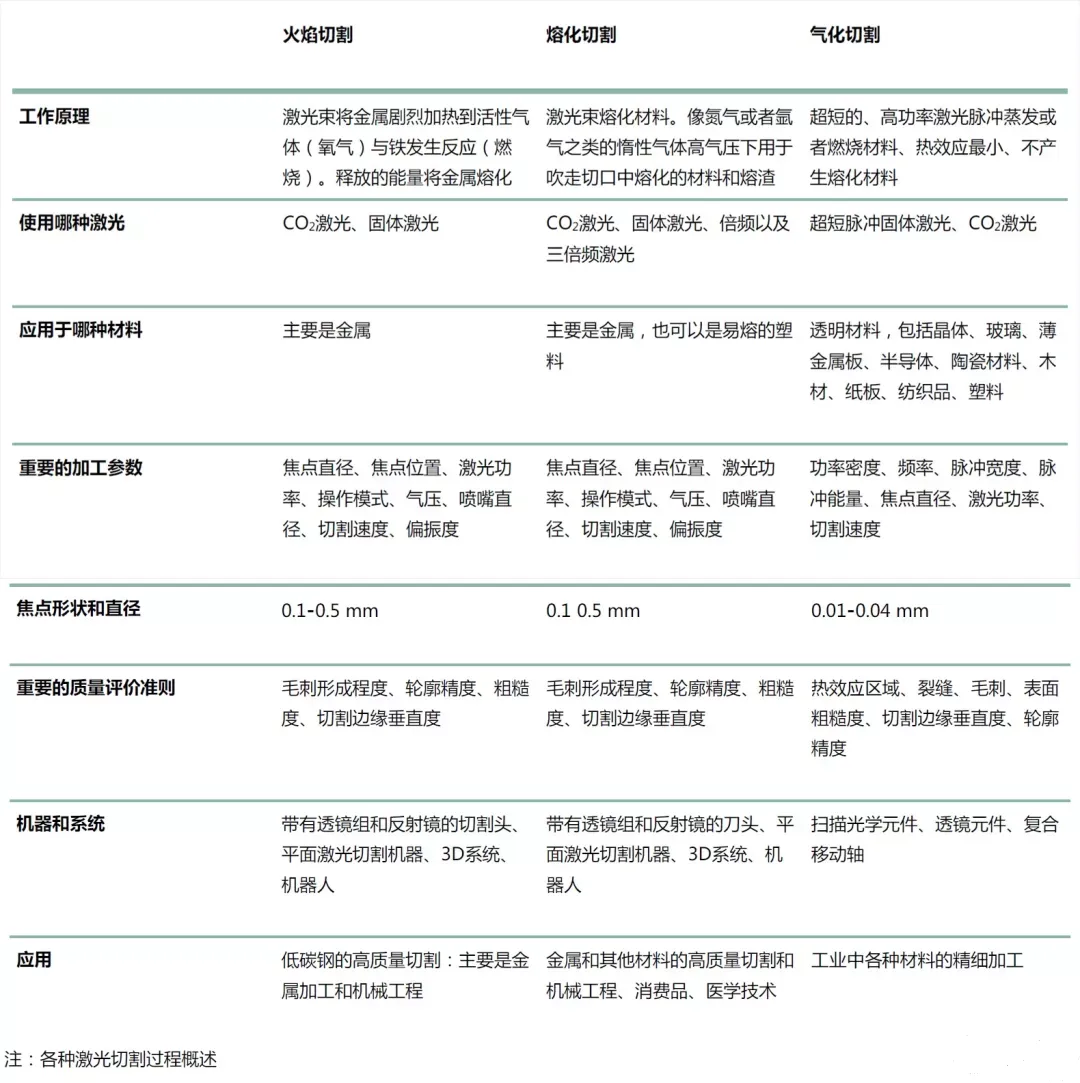
-End-
☞Source: World Advanced Manufacturing Technology Forum ☞Editor-in-Chief: Shao Yujie ☞Reviewer: Wu Xiaolan ☞Media Cooperation: 010-88379790-801 ☞Metal Processing Magazine's only submission site: http://tougao.mw1950.cn/
Disclaimer: If the video, picture, text used in this article involves the copyright of the work, please inform us at the first time, and we will confirm the copyright and pay the remuneration according to the national standard or delete the content immediately according to the supporting materials provided by you!