Laser welding
Release Date:2024/07/30
Laser welding is an efficient and precise welding method using high energy density laser beam as heat source. Laser welding is one of the important aspects of the application of laser material processing technology, its principle is to melt the workpiece by controlling the width of the laser pulse, energy, peak power and repetition frequency and other parameters to form a specific melt pool. As laser welding is a welding method with high quality, high precision, low deformation, high efficiency and high speed, with the improvement of high power CO2 and high power solid YAG laser and fiber transmission technology, and the successful development of metal molybdenum welding bundling objective, etc. Make it more and more widely used in machinery manufacturing, aerospace, automotive industry, powder metallurgy, biomedicine, microelectronics industry and other fields.
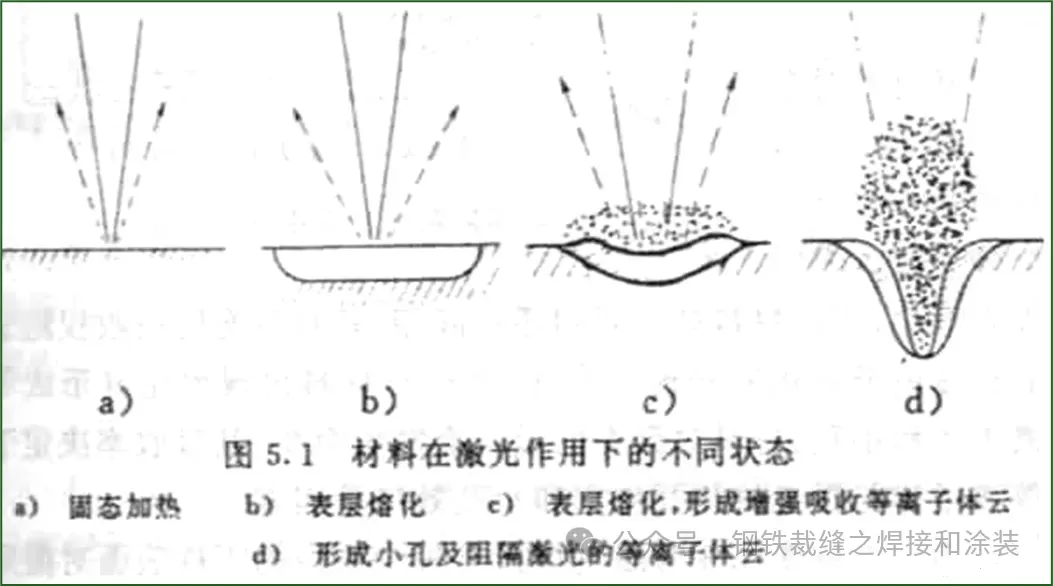
Principle of laser weldin
The commonly used laser sources for laser welding are gas CO2 laser and solid YAG laser. According to the size and working state of the laser output power, the laser working mode has continuous output mode and pulse output mode. The power density of the focused laser beam irradiated to the weldment surface is generally 104 ~ 107W/cm2.
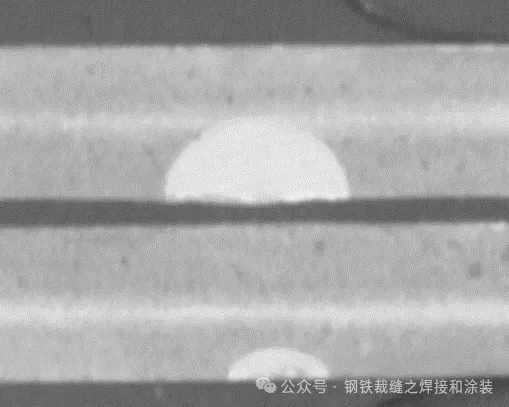
Laser deep penetration welding relies on the small hole effect, so that the laser beam of light energy to the deep material, laser power is large enough, the hole depth increases, with the laser beam relative to the welding part of the move, the metal liquid solidifies to form a weld, the weld is narrow and deep, its depth to width ratio can reach 12:1.
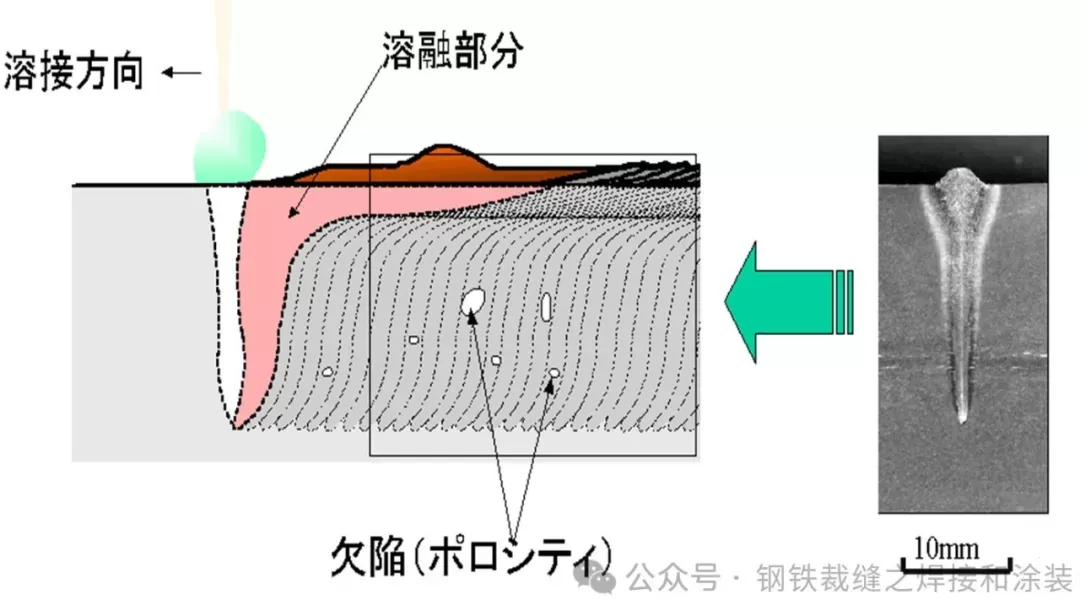
These two welding mechanisms are selected according to the actual material properties and welding needs, and different welding mechanisms are obtained by adjusting the welding process parameters of the laser. The most basic difference between the two methods is that the surface of the former molten pool remains closed, while the latter molten pool is pierced by a laser beam into a hole.
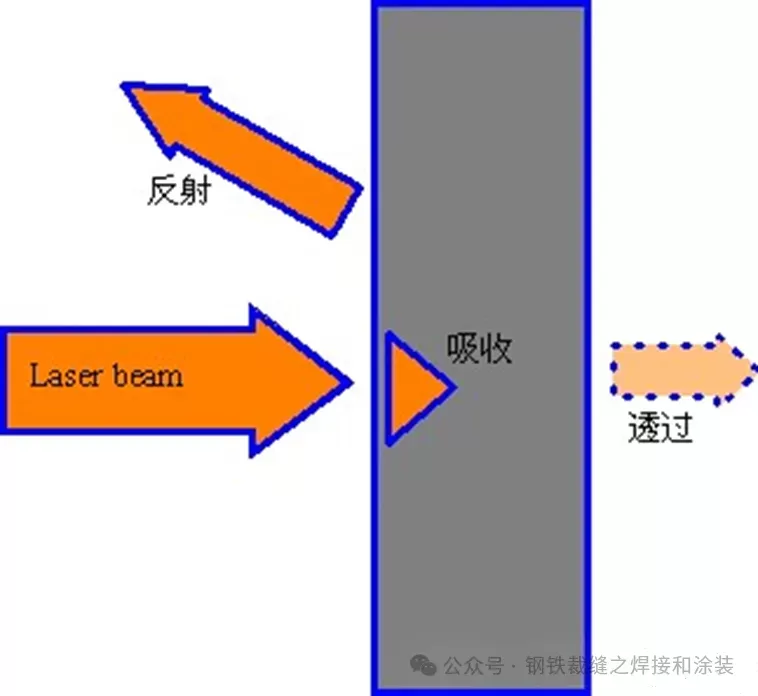
Laser welding characteristics
The advantages of laser welding are that it has low heat input, small welding deformation, is not affected by electromagnetic fields, and is very suitable for the welding of miniature parts and parts with poor accessibility. Therefore, laser welding has been successfully applied to the precision welding of micro and small parts, and the welding quality is higher than that of traditional welding methods.
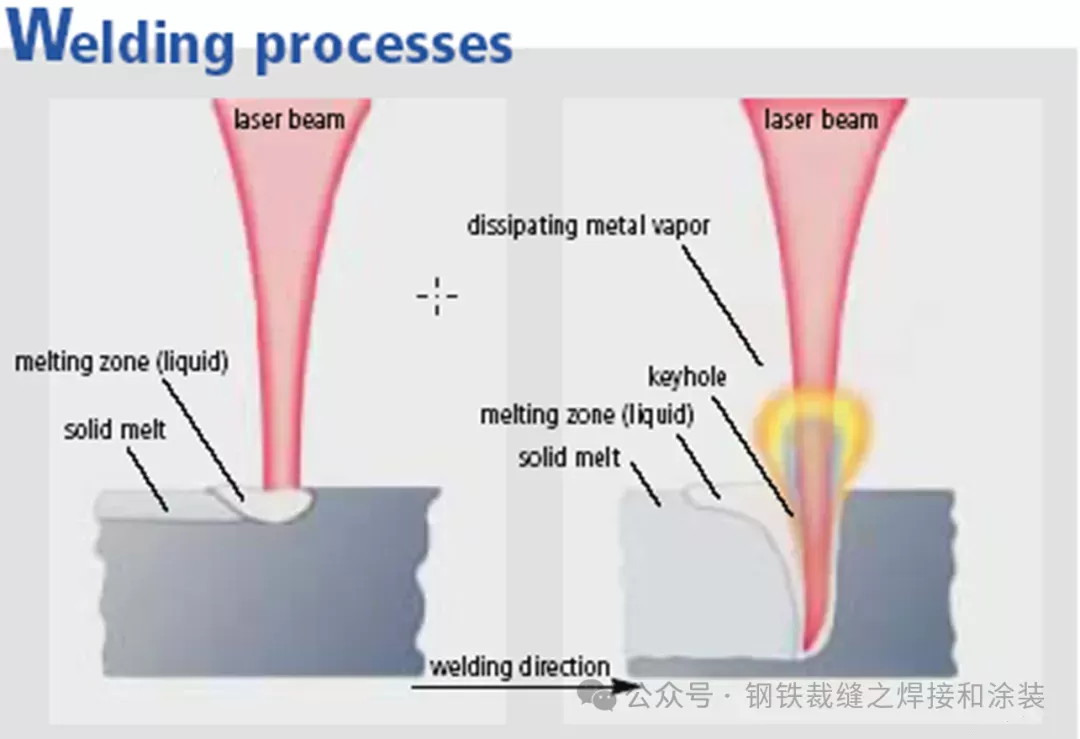
2. Weaknesses
Although laser welding is a new type of welding method, it has a good prospect, but it also has its own limitations.
(1) Welding thickness is limited, suitable for thin material welding.
(2) The clamping requirements of the workpiece are relatively high, and the gap is as small as possible. And the position of the beam on the workpiece should not be significantly offset. This is because the spot size after laser focusing is small, the weld is narrow, and the metal material is filled. If the workpiece assembly accuracy or beam positioning accuracy can not meet the requirements, it is easy to cause welding defects. In addition, the cost of precision welding fixtures is relatively high.
(3) Positioning should be very accurate, and the requirements for programming are relatively high.
(4) High reflective and high thermal conductivity materials such as aluminum, copper and its alloys, etc., will have an impact on weldability;
(5) The rapid solidification of the weld is not conducive to the discharge of gas, and there may be porosity and embrittlement;
(6) The equipment is expensive, for small batch production or complex positioning, the production price ratio of complex processes is not high.
Classification of laser welding
1. Laser deep penetration welding
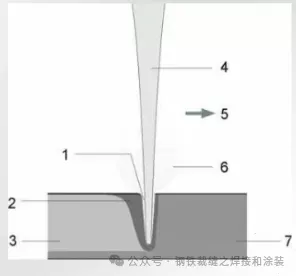
1. Keyhole 2. Molten metal 3. Weld 4. Laser beam 5. Welding direction 6. Metal steam 7. Workpieces
Laser welds are narrow and thin, and the depth-to-width ratio can even reach 10:1.
2. Laser heat conduction welding
The laser beam travels along the edge of the material, and the molten material fuses with each other and solidifies to form a weld. Weld depth from near zero to a millimeter. The thickness of the material will not exceed 3mm, usually under 2mm.
1. Melt material 2. Weld 3. Laser beam 4. Welding direction 5. Workpiece
Laser welding process parameters
1. Power density P
The size of the laser power is the preferred parameter of laser welding technology, only to ensure sufficient laser power, in order to get a good welding effect.
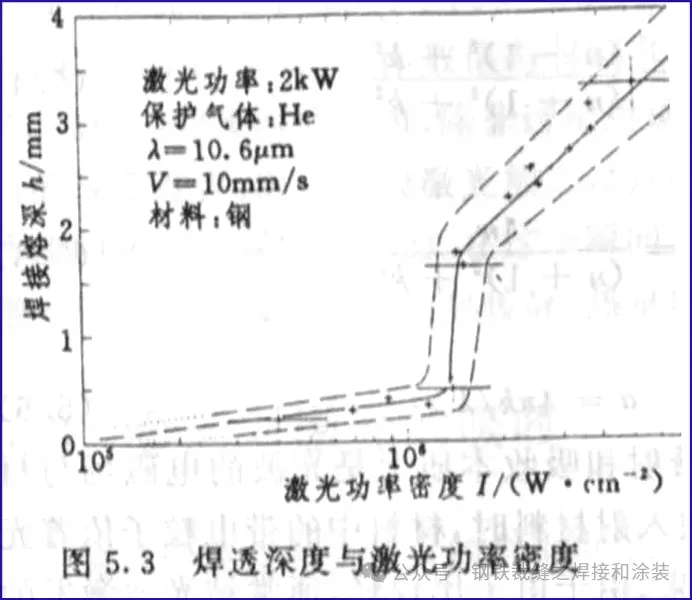
2, laser pulse waveform
Laser pulse waveform is an important problem in laser welding, especially for wafer welding. When the high-intensity laser beam is fired at the surface of the material, the metal surface will be reflected and lost by 60-98% of the laser energy, and the reflectivity changes with the surface temperature. The reflectance of metals varies greatly during a laser pulse.
3, laser pulse width
Pulse width is one of the important parameters of pulsed laser welding, which is not only an important parameter that is different from material removal and material melting, but also a key parameter that determines the cost and volume of processing equipment.
In laser heat conduction welding, the laser pulse width is directly related to the depth of the weld, that is, the pulse width determines the depth of the material melting and the width of the weld. It has been documented that the depth of penetration increases with the 1/2 power of the pulse width.
4. Laser pulse repetition frequency
In heat conduction welding, the laser emits a repetition frequency laser pulse, and each laser pulse forms a melt spot. Such as the sealing of instruments, meters, batteries, relays, plates, pipe fittings or the welding of electronic parts and mechanical parts that need to be connected mostly use this method
5, welding speed
Under certain conditions, the speed v is reduced, the line energy is increased, and the welding penetration is increased. However, if the speed is too low, the melting depth will not increase indefinitely, but the melting width will increase.
Metal melting too much, metal steam pressure is not enough; An increase in metal vapor results in an increase in plasma concentration.
6, the influence of defocusing amount on welding quality.
Laser welding usually requires a certain defocus, because the power density of the center of the spot at the laser focus is too high, and it is easy to evaporate into holes. The distribution of power density is relatively uniform in each plane away from the laser focus
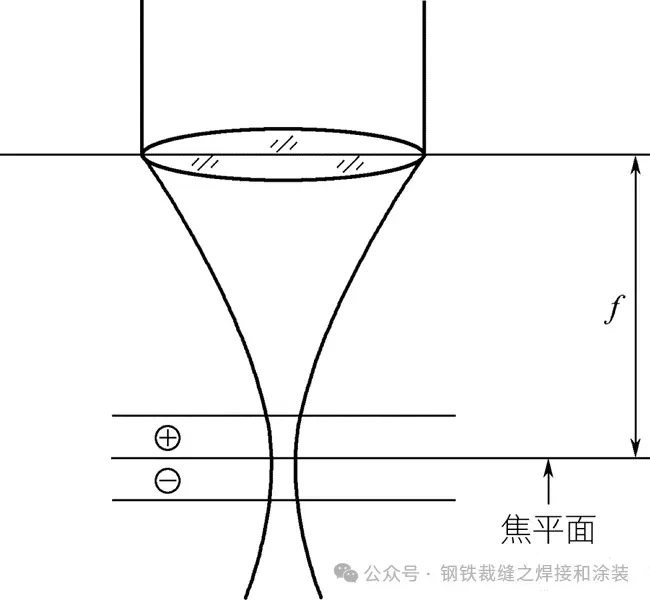
7. Gas protection
The function is to protect the molten pool and inhibit the plasma. Protection gas type: Ar, He, mixed gas gas protection mode: coaxial top blowing; Off-axis blowing; Drag cover + coaxial.
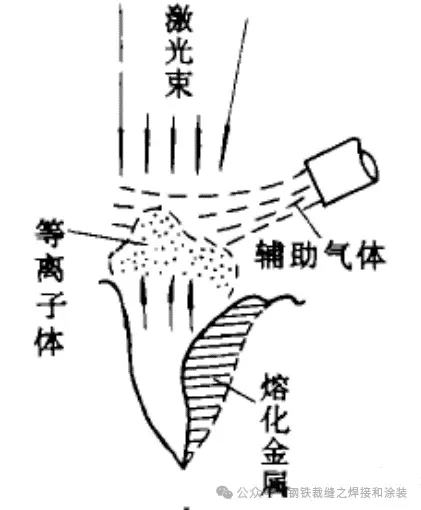
Laser welding applicable materials
1. Carbon steel and ordinary alloy steel In general, carbon steel laser welding effect is good, its welding quality depends on the impurity content.
Sulfur and phosphorus in the material are sensitive factors for welding cracks. If the content of sulfur and phosphorus is high, it is not suitable for laser welding. Medium and high carbon steel and ordinary alloy steel can perform good laser welding, but it requires preheating and post-welding treatment to eliminate stress and avoid crack formation.
2. Stainless steel laser welding Under normal circumstances, stainless steel laser welding is easier to obtain high-quality joints than conventional welding.
The low thermal conductivity of stainless steel makes it easier to obtain deep penetration and narrow weld. Stainless steel is mainly divided into ferritic stainless steel (joint embrittlement), austenitic stainless steel (hot cracking), martensitic stainless steel (poor weldability), duplex stainless steel (welding affected zone is easy to embrittlement).
3. Die steel
S136, SKD-11, NAK80, 8407,718,738, H13, P20, W302, 2344, etc.
4. Laser welding of aluminum alloy
Because of the high reflection and high thermal conductivity of aluminum alloy surface, laser welding aluminum alloy has a certain difficulty. For laser welding of high inverse materials, the performance of energy threshold is more obvious.
5. Welding of copper alloy
Similar to aluminum alloy welding, but mirror-like copper reflection performance is stronger. The most commonly used grades in industry are T1, T2 and T3, which are purplish red in appearance, so they are also called copper. Prone to welding defects: non-fusion and non-penetration (laser beam with high energy density), welding deformation, hot cracking (in the crystallization process, due to the distribution of low melting point eutectic crystals in the dendrites or grain boundaries
6. Laser welding between different steels
The extremely high cooling rate and small heat-affected zone of laser welding create favorable conditions for the compatibility of materials with different structures after the melting of many different metals.
7. Titanium, nickel, tin, copper, aluminum, chromium, niobium, gold, silver and other metals and their alloys, and steel, Kovar alloy and other alloys of the same material welding.
8. Used in the welding of various dissimilar metals such as copper-nickel, nickel-titanium, copper-titanium, titanium-molybdenum, brass-copper, low carbon steel-copper, etc.
6. Laser welding requirements
Prior to welding, it is required to clarify the customer's welding requirements, which are generally the strength of the weld (penetration requirements, porosity control requirements, crack control requirements, etc.), appearance (the flatness of the weld, the degree of oxidation, the depth-width ratio, etc.), and air tightness (bearing air pressure).
1. Weld geometry
The purpose of any quality inspection is to confirm whether the performance of the workpiece can meet the requirements of use. For welding, the quality standards of laser welding are mainly concentrated at the weld and the welding heat affected zone.
Basic requirements
Welds need to meet two basic quality requirements:
Other welding standards and defects are included in the welding process specification. The following figure shows different welding defects:
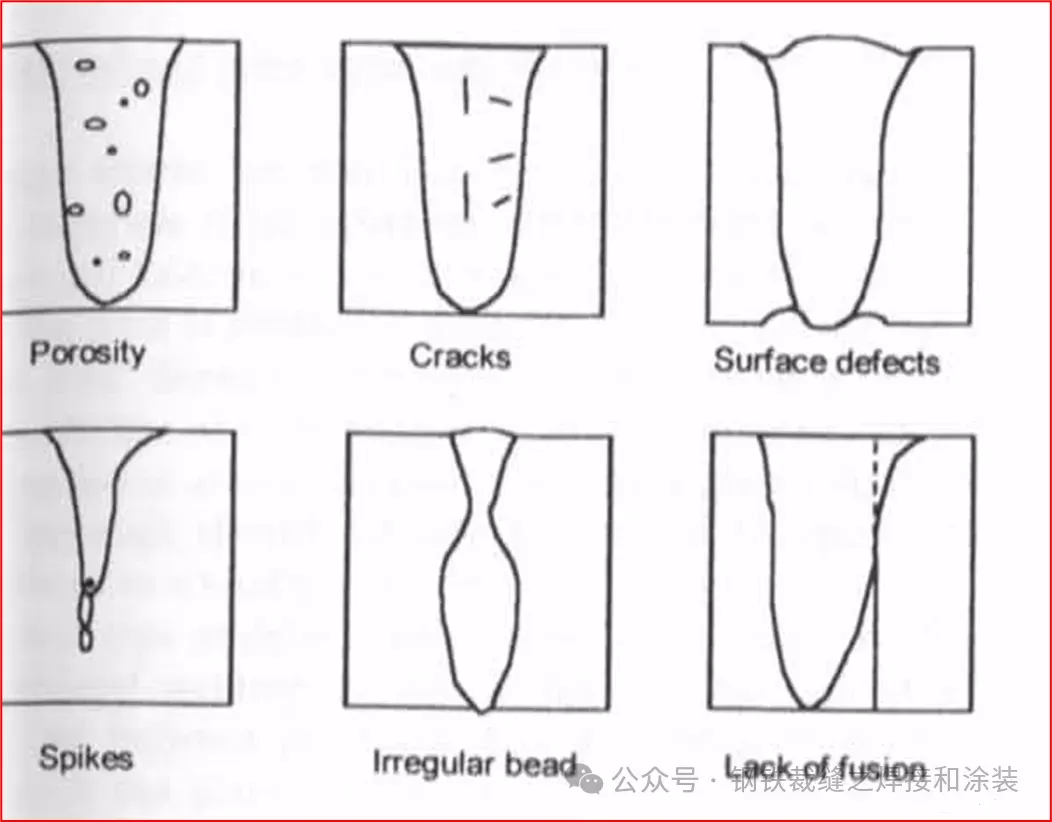
1) pores 2) cracks 3) surface defects 4) welding nails 5) irregular forming 6) failure to fuse
3. Weld internal defects:
Typical internal weld defects:
1) Non-fusion: the weld gap is too large
2) Stomata: Two types of stomata:
- Metallurgical pores
•H porosity, similar to conventional welding methods such as arc welding
- Hole
• Laser deep penetration welding itself is closely related to the instability of small holes
• The mechanism is still not well understood
3) Crack: On the surface or inside of the weld, before the weld is completely solidified, the intercrystalline plastic deformation capacity at the high temperature stage during the cooling and solidification process of the weld is not enough to withstand the plastic stress at that time, resulting in more cracks in the weld center line and heat affected zone, so those materials with a wide crystallization temperature range and high C, S and P content are prone to crack. Such as aluminum alloy laser welding process is easy to produce such cracks.
For high C steel or some high alloy steel, cold crack is also a defect easily produced in the laser welding process. Because the cooling speed of laser welding is very fast, this kind of steel is easy to get hardened structure in the weld because of the high C content, and it is easier to produce cold cracks.
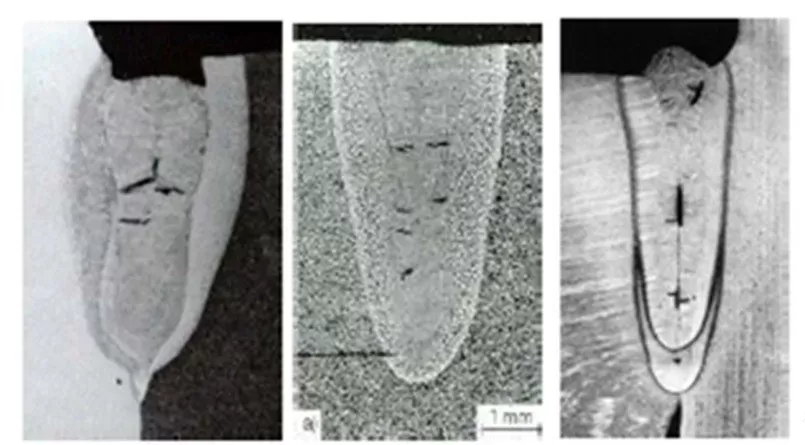
4. External welding defects:
a. Uneven weld shape: such as micro-cracks caused by the collapse of the weld.
b. Molten metal spatter: Due to the "explosion" of molten metal in the weld surface to form a pit, reduce the strength of the weld and even form pores.
c. Weld surface collapse and weld bottom depression: reduce the effective force area of the weld and reduce the strength of the weld.
d. Wrong edge: In the butt weld, the wrong edge leads to the reduction of the effective weld area.
e. Arc pit: reduce the effective force area of the weld.
f. Oxidation: Reduce the antioxidant capacity of stainless steel.
g. Splash: splash objects fall on the weld or workpiece surface to reduce surface quality and increase subsequent processing work.
h. Heat input leads to welding deformation. In the welding process, the heat inside the weld will be transmitted to the workpiece around the weld resulting in a small amount of deformation.
The development trend of laser welding
• Continuous improvement of laser devices
- Laser welding of aluminum alloy and other materials has been solved
- The depth to width ratio is larger, thicker and faster
• Numerical control system
- One-dimensional weld → two-dimensional weld → three-dimensional weld
• Development of laser composite welding technology
- Laser arc, laser plasma, laser induction, double beam
• Complete quality control
- Before, during and after welding
In short, although laser welding has many advantages, the application of laser welding technology has not been widely popularized due to the high price of lasers and low electro-optical conversion efficiency. However, China's laser welding technology has been at the world's advanced level, with the use of laser forming more than 12 square meters of complex titanium alloy components technology and capabilities, and has been invested in a number of domestic aviation research projects in the prototype and product manufacturing. In the 21st century, the demand for semiconductor wafers and various integrated circuits will be an amazing number, as a bridge connecting integrated circuits and silicon wafers, laser welding in the application of wafer packaging technology, in order to meet the increasingly miniaturized integrated circuits, high-speed, high-density, multi-pin, long life and many other needs, laser welding technology will also be its outstanding advantages.